连续冲压模具的基本知识与应用技巧
作者:佚名|分类:百科常识|浏览:86|发布时间:2025-03-12
随着五金制造行业工人工资水平的持续上涨,降低冲压生产的人力成本已成为制造商亟待解决的问题。在众多解决方案中,采用连续模是较为常见的方法之一,因为它能够有效构建低成本且高效率的自动化生产线。然而,由于连续模需要高度精确和复杂的部件设计,在实际应用过程中存在诸多挑战。
首先,当冲压模具包含较多小孔时,小型凸模不宜过长。这种情况下,可以通过将不同尺寸的凸模制成阶梯式来解决,以避免所有凸模同时承受最大压力,并减少对设备的要求。值得注意的是,较小的凸模需要制造得更短一些,而较大的则可以做得稍长些,两者之间的高度差应等于板材厚度。
其次,在连续模具中增加挡料、侧刃等步距定位装置是必要的。通过这些装置确保条料能够准确地进入下一道工序,这对于保证产品质量至关重要。常用的定位方法包括固定式挡料器和移动式的侧边调整器。
再者,为了防止材料在冲压过程中因切屑飞溅而受损或影响模具的稳定性,在设计时应加入防跳屑结构。这可以通过改进刀口形状、添加吹气孔等方式实现,确保废料不会干扰到工件表面的质量和成品率。
另外,连续模中的载体设计也是一个关键环节。由于各工序间的零件传输依赖于带材上的搭边余料(即载体),因此其稳定性直接关系到整个生产过程的精度和效率。为了保证足够的强度和刚性,通常会采用加大搭边尺寸或使用双面载体等方式。
此外,在连续模具的设计中,快速拆装功能及零件防呆设计同样重要。这有助于在维修过程中迅速更换损坏部件,并避免因操作失误导致的额外损失。
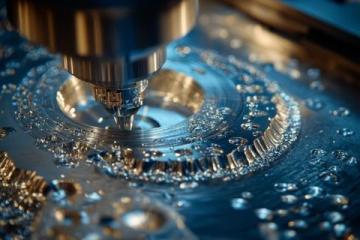
以上就是关于提高五金制造领域冲压效率的一些方法和建议。如果您对此话题感兴趣或有相关疑问,欢迎随时留言交流!
(责任编辑:佚名)